Lean management has its roots in production systems aimed at efficiency and continuous improvement. An essential tool in this system is the Andon board. It serves as a visual aid that provides real-time feedback on the production process and highlights problems as they occur. But where did this revolutionary method originate, and how has it evolved over the years?
The Toyota Production System and the Introduction of Andon
The history of the Andon board is closely linked to the Toyota Production System. This system was a response to the need to use resources more efficiently and optimize production processes. Toyota introduced the concept of visual control to better monitor the workflow on the production line. The Andon board, as a central element of these visual control systems, allowed workers to recognize and respond to problems immediately.
Visual Control and Real-Time Feedback
A key feature of the Andon board is its ability to provide real-time feedback. When a worker on the production line identifies an issue, they can press a button that triggers a signal on the Andon board. This immediate feedback enables teams to quickly address problems, whether they are related to quality, machine downtime, or material shortages. This concept of error detection and immediate response is a cornerstone of Lean principles and reflects the value of Gemba (the place where work happens) and Kaizen (continuous improvement).
Andon in the Context of Modern Lean Management
Over time, the Andon board has evolved from a simple light signal to a more complex system that offers various types of feedback and data integration. It is not just a tool for Japanese manufacturing but has gained recognition worldwide. When combined with other Lean principles, such as workplace standardization, the Andon board plays a crucial role in promoting process improvements and striving for perfection in production.
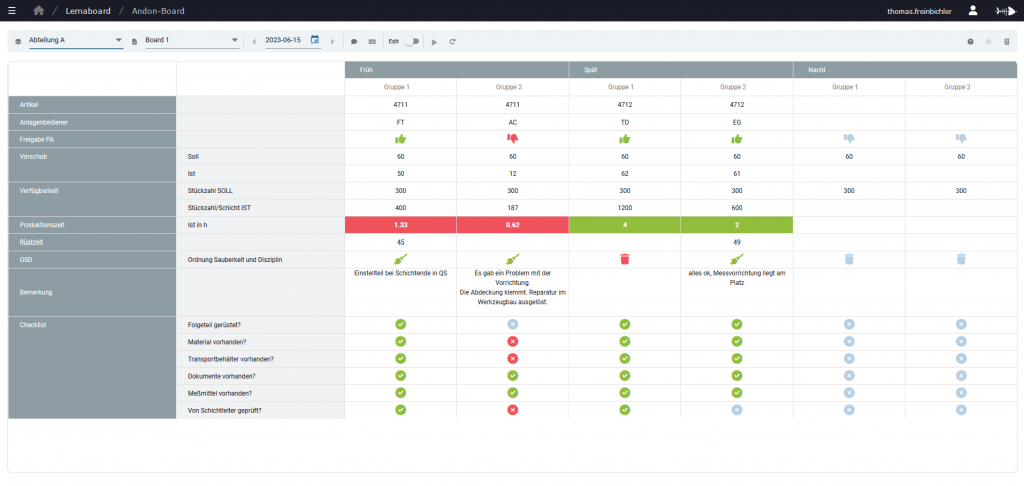
Stickfish Andon App
The “Andon” app from Stickfish Software expands the content of traditional Andon boards with symbols, default values, actual values, imported data (MDE, BDE, MES, ERP, etc.), as well as elements like dropdowns and text boxes for free text. This innovative approach allows Andon boards to be used for countless applications. Whether for capturing production data, using checklists, managing cleaning schedules, or scheduling personnel, the app offers the necessary flexibility.
The core of every Andon board is the signal element, which ensures clear communication. The app preserves this crucial function but significantly enhances it. You can define any columns and rows and integrate different variables and content to create customized displays that meet current requirements. One of the effects is the avoidance of many distributed Excel spreadsheets – the real-time evaluatable boards can be used at every workstation and displayed on large screens. In total, documentation is simplified, evaluation time is reduced, and efficiency is increased.
Conclusion
In conclusion, the Andon board is more than just a tool. It embodies the philosophy of Lean management and its dedication to quality, efficiency, and continuous improvement. It serves as a bridge between shopfloor workers and management, promoting a culture of responsibility and commitment to excellence. The Andon board, with its deep roots in the Toyota Production System, remains an indispensable instrument for companies striving for operational excellence.